LOOP X SVENSSON
A material innovation.
BACKGROUND
Sustainable production has always been the core of Svenssons business. Reducing and minimizing residual material is a producer's responsibility, but no matter how much they minimize it, residue will always occur. This project is about investigating the potential in Svensson’s cut-offs, a waste product that is too good to be wasted.
CHALLENGE
This project was a logistic project as much as a material development project. We wanted to treat the cut-off waste stream as a raw material stream, and therefore we had to implement a lean way of seizing it straight from production.
SOLUTION
Simultaneously as we developed a thermoformable material with the cut-offs as a base, we developed a block chain from seizing and sorting the material, shredding and treating it, to producing it into its new final shape. After iterations and feedback from global design brands and architects, we finely tuned it into its final appearance and characteristics.
RESULT
The material itself is a thermoformable material, ready for further transformation in the felt product category. By seizing the material straight from production, we know exactly what it contains, where it comes from, what certifications it fulfils and the social impact that the producer contributes.
Made / saved / Remade in Sweden
There is a global need for a system change in order to achieve circular businesses. We need to minimize our footprints by not only reducing our waste but starting to see it as a resource, because only then can we say that a product is truly resource efficient.
We saw an opportunity in making use of residual textile fibers from production and utilizing their unique properties and characteristics, extending their lives by circulating them into a new kind of material. In collaboration with Svensson, we ensure locally produced textiles with Ecolabel certification and flame retardant properties.
We’re entering an era where resources no longer seem to be infinite, and we have to start looking at them differently. When does something lose its value? Or does anything really lose its value? This collaboration shows that it is possible to achieve a system change, resulting in a world class design material.
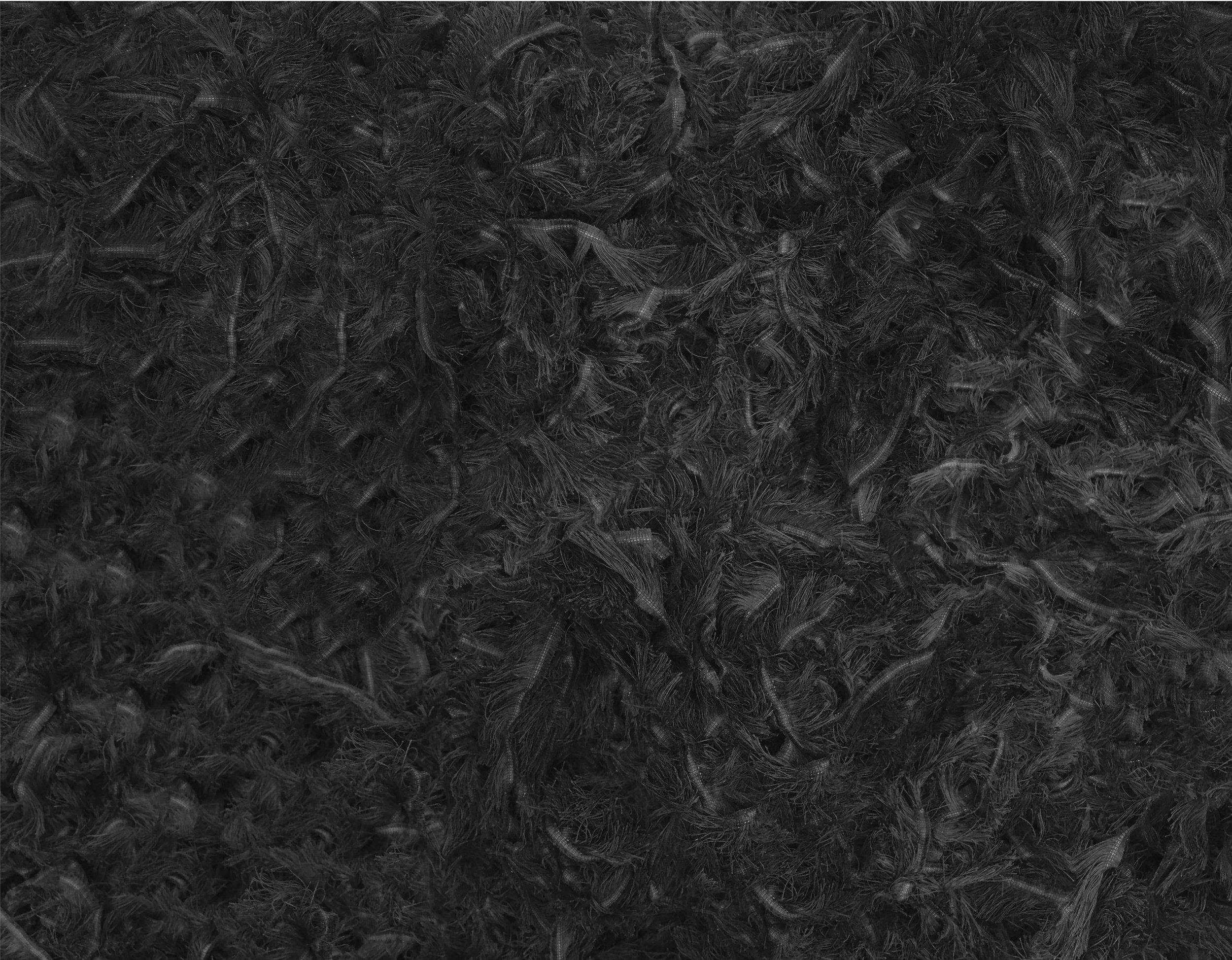
A holistic logistic
Reducing and minimizing residual material is a producer's responsibility, but no matter how much they minimize it, residue will always occur. What matters then is what you do with it.
The positive thing about using textile residue is that the material is completely unused and has the same unique qualities and properties as the actual textile. We know exactly what it contains, where it comes from, what certifications it fulfils and the social impact that the producer contributes. This is the recipe to achieve a circular system. Transparency is key.
The environmental profit of the product is very straightforward.
Firstly, there is no need for producing new fibres. The cut-offs will always occur because of how the looms are built, and this secures a continuous flow which closes the system.
Secondly, there is full control of what the fibres contain. Since the original fabric is Ecolabel certified, flame retardant and locally produced, so are the saved textile fibres.
Thirdly, the fibres are already coloured and don’t need another round.
Last but not least, we have total control of the logistics chain, from raw material to the customer’s shelf.
A material innovation
This project took its shape by combining curiosity with materials and process know-how developing a proof of concept in The Loop Factory Lab. After iterations and feedback from global design brands and architects, we finely tuned it into its final appearance and characteristics. Textile fibres play an important role, in terms of both aesthetics and function. We need them to stitch together and create a sturdy material, and we need them to tell a story. Looking at the fibres individually, they are all different. Looking at them united, they create a whole.
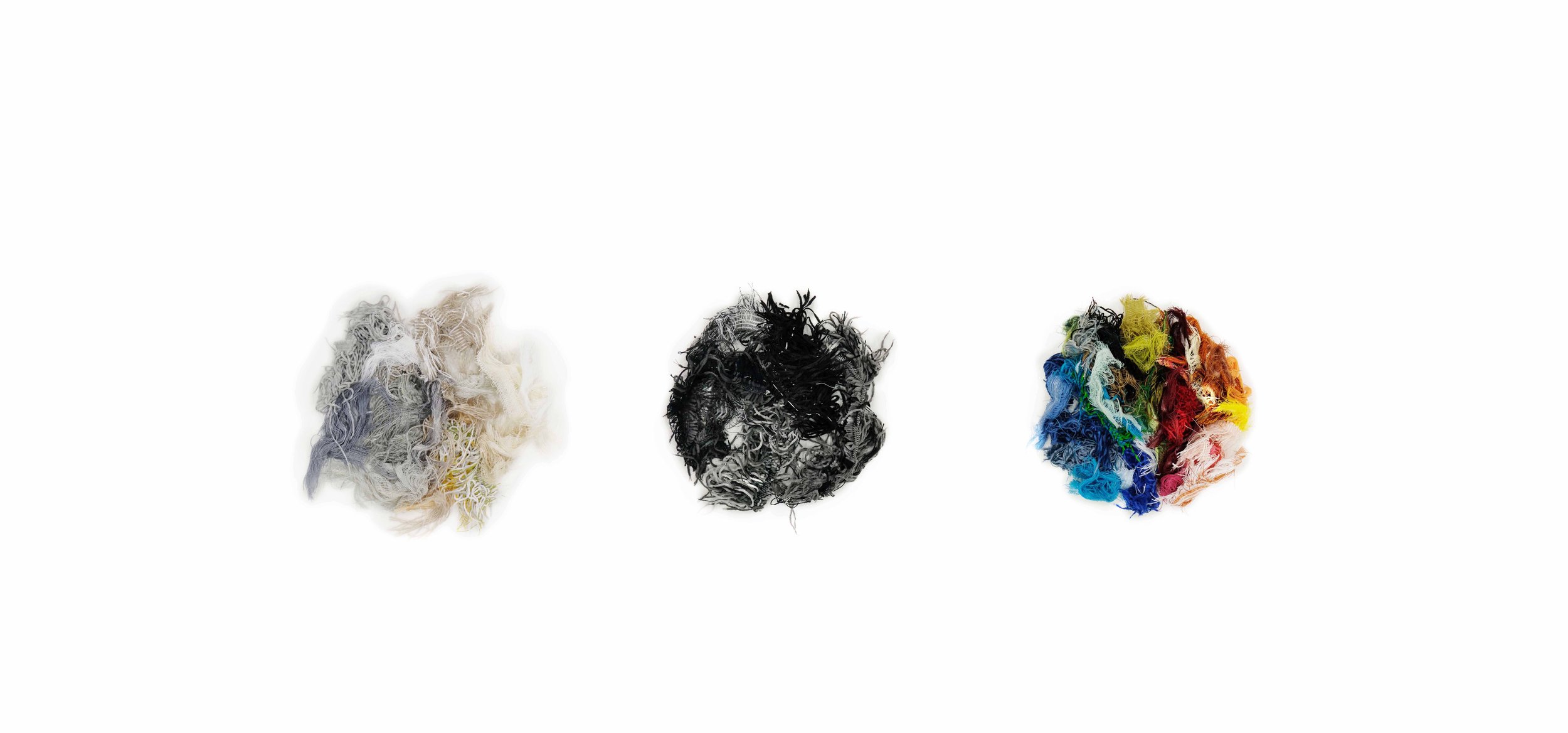
True colors
Though there are a lot of textile residues to save, it is the industries that decide what colours our raw material will have. Using a specially designed sorting system, we created unique colour schemes to ensure quantities for industrial processing. The colour composition’s variety is a direct reflection of reality. The variety is industrially natural, and the tints give the material meaning and identity.